What Is OEE?
Overall equipment effectiveness (OEE) was invented in the 1960s by Seiichi Nakajima, the founder of the Total Productive Maintenance (TPM) system. OEE is a key performance indicator (KPI) calculated by manufacturing companies to measure manufacturing performance.
The OEE indicator is expressed as a percentage from zero to 100. A score of 100% means the manufacturing unit is operating at full capacity:
- 100% quality (producing only good parts)
- 100% performance (manufacturing as fast as possible)
- 100% availability (no stop time)
OEE calculation and improvement are critical for any industrial company, especially capital-intensive industries, such as:
- Automotive
- Aerospace
- Food and beverage
- Packaging
- Heavy machinery
The OEE improvement is critical for driving improved efficiency, higher quality and reduced cost.
Although the concept is simple, companies apply this calculation in different ways. The reasons for differing formulas can vary, such as lack of data availability, unique line details or even management preference.
The complexities are not in the calculations themselves but mostly in the challenges of obtaining reliable machine and process data. Equally challenging is integrating machinery and other tools to transform the data into information that can improve actions and performance.
In this article, we will examine:
- How to calculate your OEE
- Practical, real-life use cases for calculating OEE
- Challenges encountered on the shop floor
The Formulas for OEE and How to Calculate Them
First, start with the calculations. The most well-known formula is:
OEE = Availability × Performance × Quality
If the equations for availability, performance and quality are substituted in the above and reduced to their simplest terms, the result is:
OEE = (Good Count × Ideal Cycle Time) / Planned Production Time
Next, break down the factors of this equation:
Availability
Availability considers all events that stop planned production. It is calculated as the ratio of run time to planned production time:
Availability = Run Time / Planned Production Time
Run time is planned production time minus stop time. Stop time is defined as the time during which the manufacturing process was intended to be running but was not due to unplanned stops (e.g., breakdowns) or planned stops (e.g., changeovers).
Performance
The performance indicator factors in anything causing the manufacturing process to run at a suboptimal rate. It calculates how far your operation is from a best-case scenario.
It is calculated as:
Performance = (Ideal Cycle Time × Total Count) / Run Time
Ideal cycle time is the fastest cycle time your process can achieve in optimal circumstances. When it is multiplied by total count, the result is net run time (i.e., the fastest possible time to manufacture the parts).
Quality
Quality considers manufactured parts that don’t meet quality standards, including parts that need rework. OEE quality is similar to the first pass yield. It defines good parts as parts that pass through the manufacturing process the first time without requiring any rework.
Quality is calculated as:
Quality = Good Count / Total Count
Interpreting Your OEE Performance
The closer to 100% you are, the better your OEE is. Displaying your OEE and your OEE components (i.e., availability, performance and quality) is the first step in drilling down your efficiency detractor.
Look at the following example of OEE data for two sequential weeks in Figure 1:
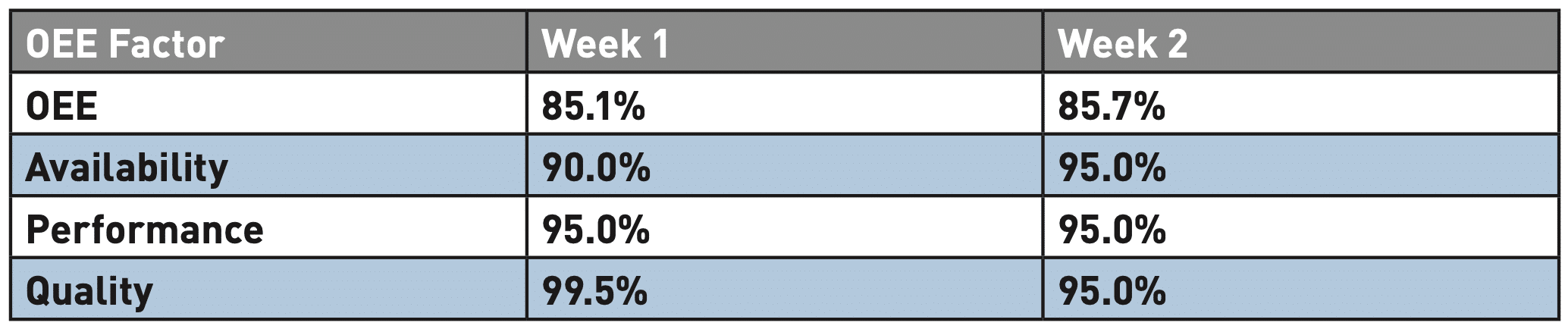
Note that OEE improved from the first week to the second. The improvement came from a better availability ratio. On the other hand, the quality yield declined significantly and requires attention.
How to Apply OEE Formulas to Collect Data and Overcome Shop Floor Challenges with deviceWISE
General Architecture
deviceWISE, powered by Telit Cinterion, simplifies the architecture, as you can see in Figure 2. It operates as middleware with features that include:
- Real-time machine data collection
- Edge logic
- Data transformation and integration
- OEE and other KPI calculations
- Database and IT connectivity
- Cloud connectivity
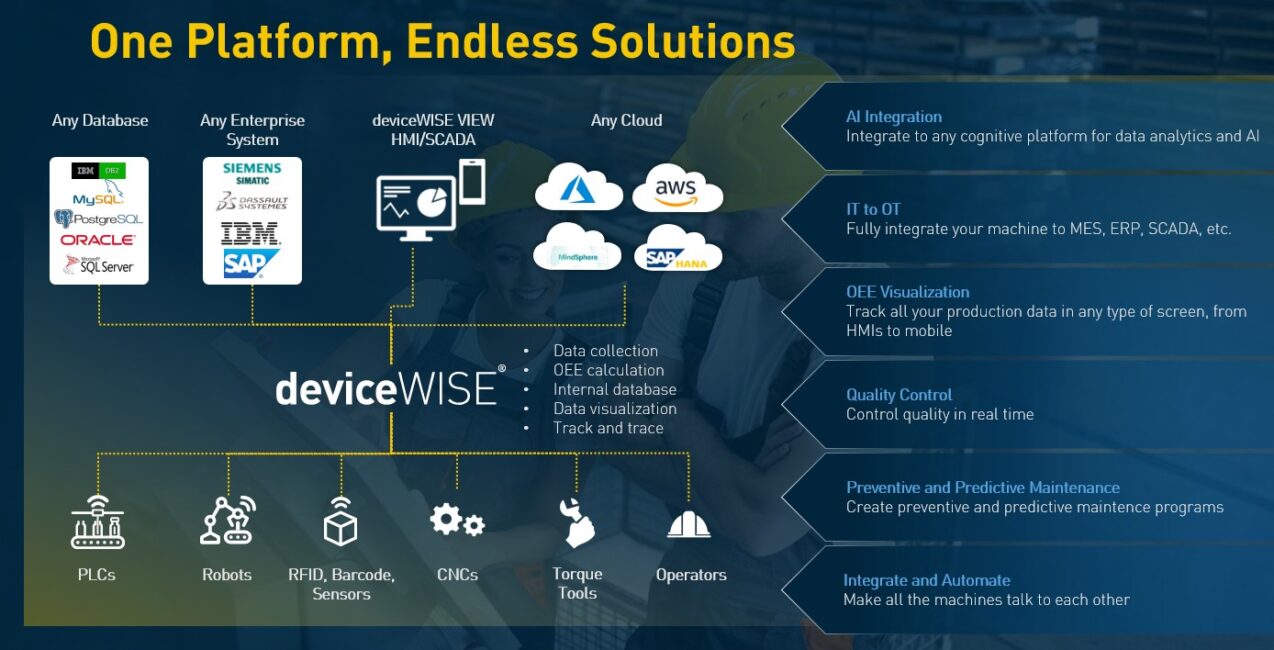
deviceWISE is a complete end-to-end industrial IoT platform. It comes with the tools needed for projects of any size. deviceWISE is used and trusted by Fortune 1000 companies. Seven out of 10 of the world’s largest car makers use it because of its versatility and cost-effectiveness.
deviceWISE provides hundreds of native industrial drivers to simplify the data collection process. Data processing can be done within deviceWISE using a visual edge logic engine. The tool comes with IT connectors for databases, MES, ERP and more. All visualization can be done without writing custom code, utilizing the deviceWISE VIEW drag-and-drop HMI and SCADA system.
The core building blocks of deviceWISE are described in Figure 3 below:
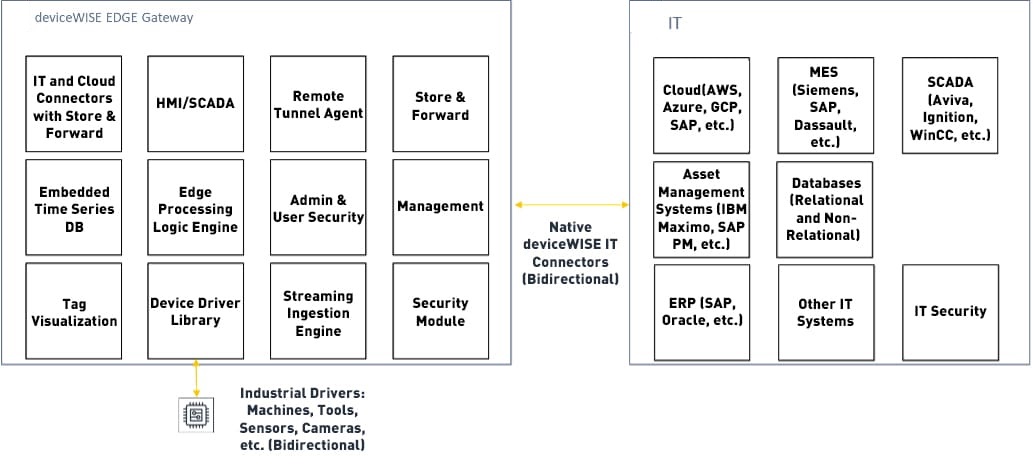
Application Diagram
The application will depend on the features to be implemented. deviceWISE allows for extensive scalability. It can be deployed as a standalone OEE solution or be integrated into a more complex environment for complete OT and IT integration (see Figure 4).
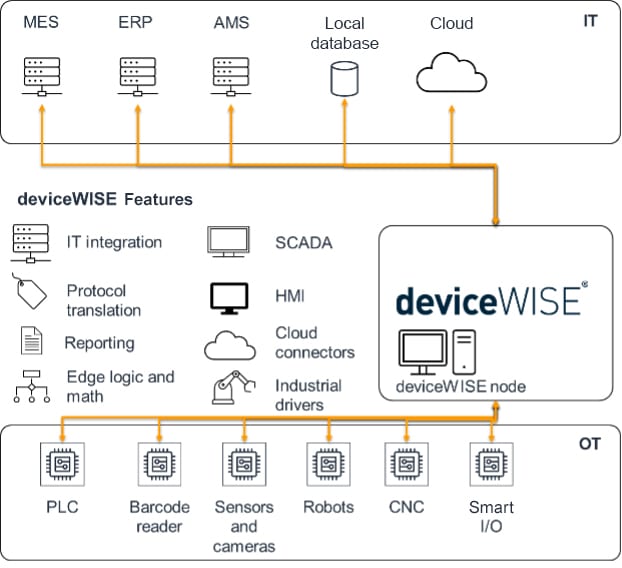
Data Collection
The first and most common challenge for an effective OEE implementation relies on data collection. Good data analytics starts with good data availability. Your team could manually collect data from the process and even use rudimentary tools like Excel to calculate your OEE. However, manual data collection is highly inefficient and inaccurate.
deviceWISE software allows you to collect real-time data from machines. Manufacturing environments use hundreds of various machines and gather data from multiple industrial protocols. deviceWISE is the most efficient protocol converter. It allows you to collect machine data using open and private protocols, as you can see in Figure 5. These protocols include:
- OPC UA and OPC DA
- Modbus
- MTConnect
- BACnet
- Siemens
- Rockwell
- Mitsubishi
- Omron
- FANUC
- Torque tools
deviceWISE comes with hundreds of drivers you can download at no additional cost.
For networked machines, deviceWISE makes data collection a simple process. It consists of choosing the driver and appointing it to the IP address. All the tags will be auto-enumerated. For machines requiring analog or digital I/O data collection or external instrumentation, deviceWISE can collect data from sensors.
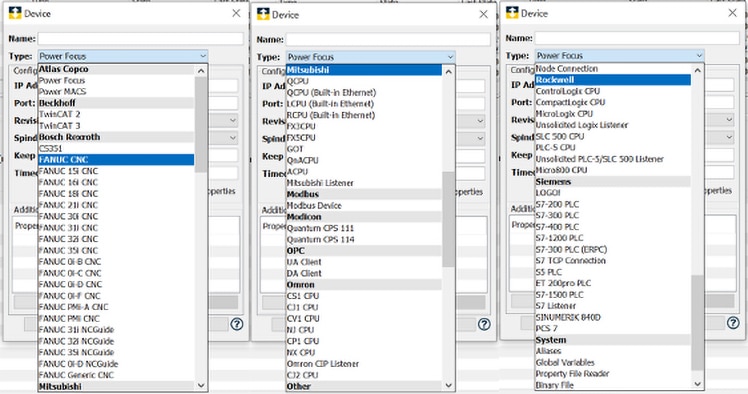
Creating the Algorithm
Using deviceWISE as an OEE tool doesn’t require custom code. With the machines connected to deviceWISE, you can set up algorithms by mapping the variables to a trigger. The logic is done with a visual logic workflow to facilitate application creation, maintenance and calculations.
You can calculate your OEE machine by machine and consolidate the calculations by line, shift and plant level to improve management visibility. You can include alarm functions for monitoring specific machine and process conditions and customize automated actions (see Figure 6).
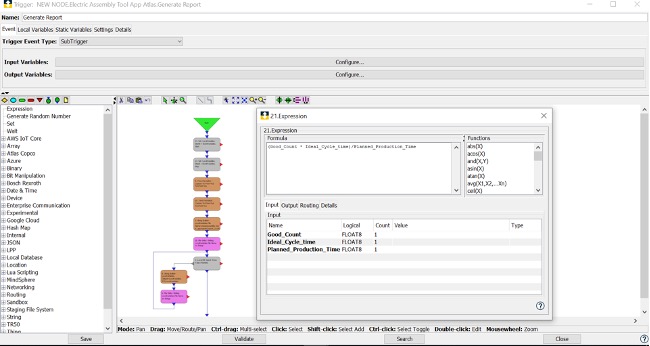
Setting the Front End
deviceWISE has a full HMI and SCADA module called deviceWISE VIEW. You can create any OEE application with simple drag-and-drop functionality. Charts, value cards and SQL tables are available to appoint the machine variable and visualize real-time and historical data (see Figure 7).
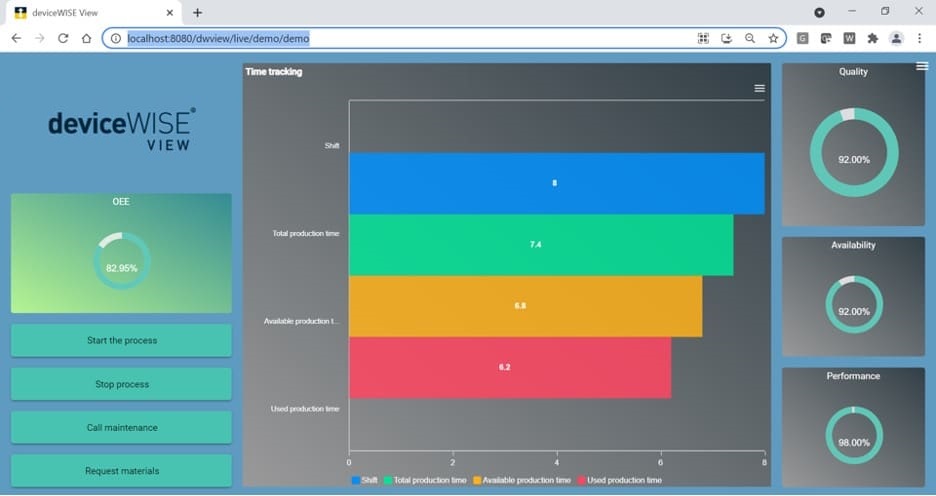
IT Integration
If required, deviceWISE can manage full bidirectional integration with databases and IT systems, such as AWS, Azure and IBM. This integration does more than deliver data to maintain a historical data record. It synchronizes and enhances major business systems built into operational technology (OT) and information technology (IT) systems that run today’s businesses. Accessing this data improves bidirectional business decision-making and integrates with OEE and its subcomponents.
Many companies use alert functions for quick operations reactions. Set up a trigger in deviceWISE and set the thresholds. If any critical production ratio requires attention:
- Messages can be shown in OEE displays
- Tickets can be opened in asset management systems (e.g., IBM Maximo, SAP PM)
- Emails can be sent to managers
Actions to Improve Your OEE
Knowing the problem is the first step to fixing it. After implementing an efficient OEE system, acting on the root causes of the inefficiencies is critical. Successful strategies to implement for various OEE reduction causes include:
- Pay Attention to the Details
Even within a manufacturing plant, it can be counterproductive to set only one OEE target. For example, if you have two identical production lines, but one line makes a single product, and the other makes 10 different products, would you expect them to have the same OEE score? No. The line making 10 products is likely to experience far greater availability loss due to changeovers and a lower OEE score.
- Reduce the Duration of Planned Downtime
With robust OT/IT integration software like deviceWISE, you can automate machine setup and reduce setup time. The software’s low latency is critical to avoid hidden downtime in the machine.
Improved process visibility provides managers with better information for planned stops. deviceWISE can calculate the machine OEE and schedule maintenance based on machine information.
- Reduce Unscheduled Downtime
Unscheduled downtime is expensive. If one machine component fails, it can halt the entire production system, resulting in the loss of production time, raw materials and more. deviceWISE can be used to learn expected machine behavior. Fully automated preventive maintenance can be triggered by identifying anomalies in the production cycle, such as:
- Power consumption
- Vibration and noise
- Temperature
- Reduce Rejects
Quality problems have a severe and direct impact on your OEE. deviceWISE can be used as a quality check system integrated with machine data, external sensors and cameras for quality control. Keep tight control of your quality yield. Use deviceWISE to provide historical quality references and trigger correction actions in real time.
Improve Your OEE Measurements with deviceWISE
OEE is not a static, individual measurement of success, failure or mediocrity. It’s a living metrics combination that points operational technologists to the levers they must pull to improve business performance. deviceWISE is an industrial IoT data management system with core capabilities, such as:
- Real-time access to operational data
- Data rationalization to identify relevant points
- Data transformation into usable formats
- Speedy delivery for ingestion by cloud and middleware OT and IT systems
OEE is only one beneficiary of these capabilities. IoT systems like deviceWISE ensure OEE’s evolution into a living operational measurement.