Gain Greater Flexibility, Lower Latency and Accelerate Time to Value with deviceWISE®
Keeping Pace in a Connected Manufacturing World
Manufacturing is undergoing a major revolution. The Internet of Things (IoT) is driving the change, using lightweight, low-power sensors to connect devices across the factory floor. Today’s industrial environments are connected and mobile, creating substantial business benefits potential. The Aberdeen Group found that 74% of best-in-class companies can collect and aggregate sensor data in real time.
Companies are monitoring and analyzing factory floor performance to improve processes and bring analytics to previously isolated data. Informed by these insights, manufacturers can examine their supply chains and processes and look for ways to accelerate innovation.
Current technologies are restricting manufacturers’ ability to realize IoT’s promise. One of the most limiting factors lies with the existing communications standards. Many manufacturers rely on Open Platform Communications (OPC). OPC has been a key interoperability standard for communications since 1996. Although useful, this aging standard by itself can’t keep pace with today’s changing needs.
Manufacturers need a better way to connect their organizations and make the most of the IoT revolution. They must quickly establish connectivity from shop floor to top floor — and their ecosystems.
The answer is deviceWISE, powered by Telit Cinterion. In this paper, you’ll learn how deviceWISE far surpasses OPC. You’ll discover why deviceWISE is ideal for manufacturers seeking to address top challenges and get ready for new ones.
Table of Contents
- Gain Greater Flexibility, Lower Latency and Accelerate Time to Value with deviceWISE ®
- Keeping Pace in a Connected Manufacturing World
- It’s Time to Think Beyond OPC
- Move Ahead with the deviceWISE Advantage
- deviceWISE vs. OPC Solutions
- See deviceWISE in Action
- Bring Home the Big Win with deviceWISE
- Key Takeaways
It’s Time to Think Beyond OPC
OPC is the standard approach for supervisory control and data acquisition (SCADA) and human-machine interface (HMI) systems to interface with programmable logic controllers (PLCs). The original OPC specification was tied to the Microsoft Windows operating system (OS). OPC Data Access (OPC DA) and Microsoft took connected manufacturing a significant step forward.
Using OPC DA in today’s manufacturing climate poses several challenges. OPC’s underlying technology is so aligned with Microsoft that it isn’t compatible with many other technologies. As OSs like Linux become prevalent in manufacturing, companies relying on OPC DA can find their interoperability plans thwarted.
Dynamics is another pain point. OPC is designed to constantly interrogate devices. It consumes significant compute time and hampers efficiency, limiting throughput and scalability. Supporting the frequent polling process requires additional servers, which creates management issues.
These traditional connectivity standards face functionality limitations. OPC DA and OPC Unified Architecture (OPC UA) focus on accessing information only from devices — nothing more. Manufacturers wanting to integrate business and enterprise logic must buy an OPC-compatible application or create one with custom code. Custom coding is time-consuming, requiring more than 60% of each project for device and enterprise IT connectivity. Custom coding depends on developers. Manufacturers are vulnerable if the original coder leaves.
Move Ahead with the deviceWISE Advantage
To overcome these limitations, manufacturers need a comprehensive platform to enable device and application communication. deviceWISE is an integrated solution to connect the factory to the enterprise and the value chain fast. This platform empowers them to unlock the data they need to improve productivity and drive growth and revenue.
deviceWISE incorporates business logic and data connectors in one package. A subject-matter expert can set up and deploy it instead of a technical IT specialist. Organizations can develop a rapid business solution with minimal technical staff. The platform integrates seamlessly with multiple enterprise systems out of the box, further enhancing business agility.
deviceWISE delivers superior performance compared to traditional communication solutions, improving device access speed and efficiency. Best of all: deviceWISE does not require custom coding for integration. Organizations can plug it in, let deviceWISE connect devices and applications, and start configuring with drag-and-drop logic.
deviceWISE vs. OPC Solutions
Look at deviceWISE’s features and capabilities and how they compare to OPC solutions:
A Comprehensive Platform
deviceWISE offers a complete platform spanning the manufacturing environment device and enterprise logic layers. In contrast, OPC addresses only the device layer. deviceWISE comes with hundreds of drivers and enables business logic in a no-code environment. It provides bidirectional connectivity to IT systems and relational and non-relational databases. deviceWISE transparently connects system to system regardless of the back-end location. This platform can interact seamlessly with third-party clouds, including:
- AWS
- Microsoft Azure
- Google Cloud Platform
- IBM Watson and Maximo
- SAP HANA
- Siemens MindSphere
Hundreds of Drivers
We understand collecting data with OPC can be a handy solution. That’s why deviceWISE comes with OPC UA and OPC DA drivers, but it’s far from enough for real-life applications. The platform comes with other open protocol standards, such as Modbus, MT Connect and more. To enable complete and efficient data collection, deviceWISE comes with a growing number of native drivers, including:
- Siemens
- Rockwell
- Omron
- Mitsubishi
- FANUC
- ABB
- Emerson
- Schneider
- Atlas Copco
- Ingersoll Rand
Real-Time Data Federation
Data extraction and processing and enterprise connectivity capabilities are integrated deep into deviceWISE. While OPC only offers data extraction, deviceWISE can aggregate and transform data into actionable information.
Faster Time to Market
deviceWISE helps manufacturers get the competitive edge they need by accelerating time to market. Factories can deploy the platform without custom code. deviceWISE enables organizations to set up manufacturing environments and pivot when changes are necessary. Deploying and applying alterations to OPC requires custom coding, which slows the process.
Flexible Deployment
Today’s manufacturers can choose from multiple vendors’ various technology solutions. To take advantage of this freedom of choice, they need a platform with total deployment flexibility. deviceWISE is compatible with multiple OSs. It operates on almost any combination of OSs, CPUs, mainframes, servers, and leading switches and routers. While OPC solutions must deploy on a Microsoft OS, deviceWISE enables manufacturers to deploy the optimal solution for their legacy equipment and business requirements.
Out-of-the-Box Enterprise Integration
Integration with existing IT systems is a component of deviceWISE. This integration allows bidirectional communication between systems and machines. These systems include:
- MES
- SCADA
- ERP
- MRP
A customer can fully integrate OT to IT with deviceWISE in a simple configuration without writing any code. In contrast, the integration available with OPC solutions is limited and demands thousands of hours to create custom code.
Low Latency
Compared to OPC, deviceWISE offers extremely low latency. Benchmark tests show data performance up to 10 times faster than the traditional protocol. With deviceWISE, latency is often near zero, so manufacturers can realize improved efficiency enterprise-wide.
In the world of industrial IoT (IIoT), latency is a critical concern. As more data is produced, the ability to collect and analyze it efficiently impacts machine productivity. If a process demands data validation, each millisecond it takes for the system to respond causes downtime. As a result of OPC replacement by deviceWISE, one carmaker increased uptime by 3,000 minutes per year in one plant. This increase created a return on investment of $90 million per year.
Latency creates unreliable data collection risks. As PLCs are designed to delete their tags each cycle, high latency systems can lose data, compromising data reliability. deviceWISE was built to solve this problem. By enabling features like unsolicited messaging, the system provides near real-time communication, which reduces network data flow and ensures data reliability.
Lab Testing in Stable Environment
Timing data scattered due to:
- Single-threaded nature of application/ communications
- PLC creates and destroys OPC tag references every time transaction is called
- PLC scan time variances
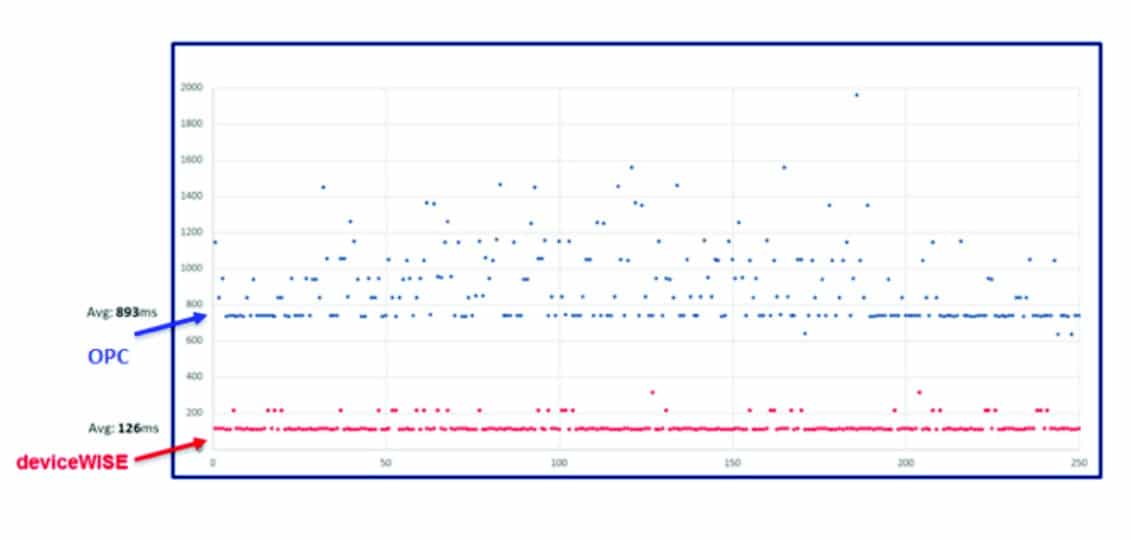
Built-In Analytics
Intelligence at the network edge is critical for IoT applications, which constantly gather real-time data. deviceWISE includes integrated edge analytics to support modern applications and IoT processes. It allows manufacturers to create sophisticated logic without requiring programming. The system enables logic workflow creation, enabling event stream logic at the edge
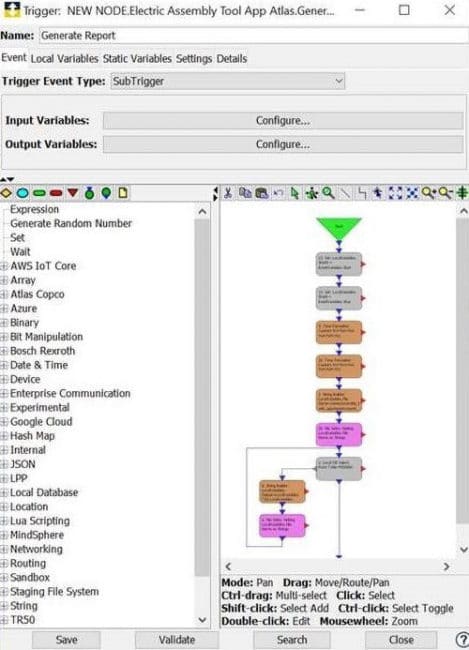
Visualization
The data you collect from your machines is essential for making intelligent business decisions. deviceWISE VIEW provides user-friendly, real-time machine data collection and visualization in a few clicks. After collecting your data, you can transform it and calculate your KPIs, create charts and more with deviceWISE VIEW. Build custom dashboards and HMIs to display on-premises or in the cloud using drag-and-drop widgets. Visualizing your factory data can help you improve business decisions by enabling you to:
- Visualize and monitor real-time and historical data
- See patterns and trends
- Analyze data with ease
- Create bidirectional applications including buttons, text boxes and other input sources
- Interpret received data
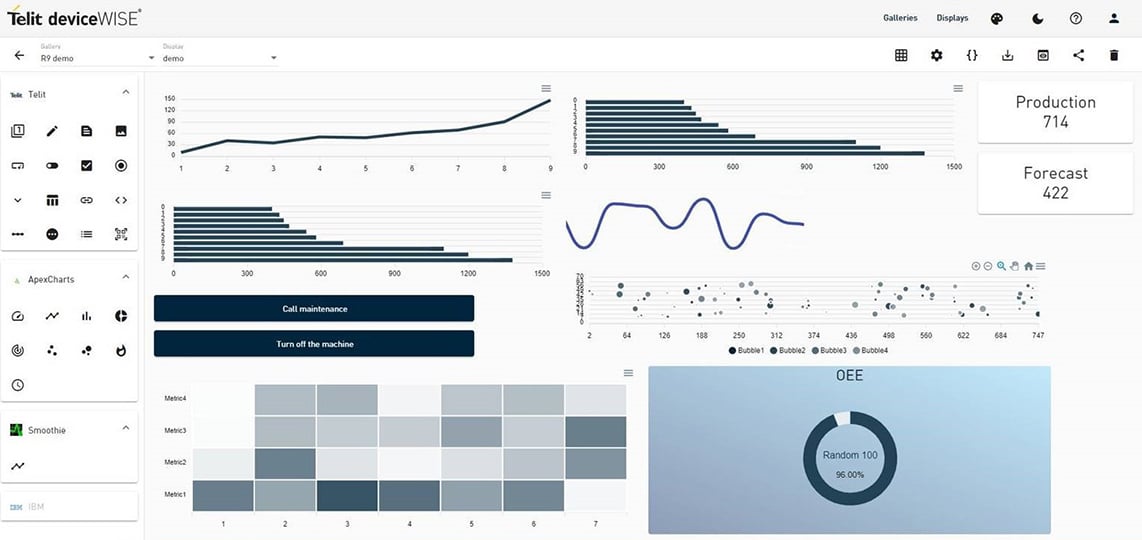
Robust Security
Security is essential in the manufacturing environment with its many endpoints and potential vulnerabilities. deviceWISE integrated, role-based security addresses today’s changing threat landscape. It is ready for Microsoft Active Directory, with out-of-the-box support for firewall, SSL and third-party authentication. OPC, in contrast, does not support Active Directory or LDAP authentication and offers limited protection.
Operations Advantage
OPC solutions require manufacturers to hire multiple third-party providers to keep up with advances in technology. With so many consultants and vendors involved, accountability can be difficult to track. The resulting friction can hamper troubleshooting and reduce business agility. deviceWISE provides manufacturers with a single contact point for development and layers. It’s a one-stop shop for questions and issues.
Lower Cost of Ownership
deviceWISE enables a lower total cost of ownership than OPC deployments. Although OPC software is inexpensive, manufacturers must add many more servers and third-party applications and vendors. Alternatively, they must create and maintain code to realize the operational and business advantages deviceWISE offers. In addition, OPC applications tend to have hidden latency costs impacting factory productivity. This cost is often represented by thousands of downtime minutes behind data polling time.
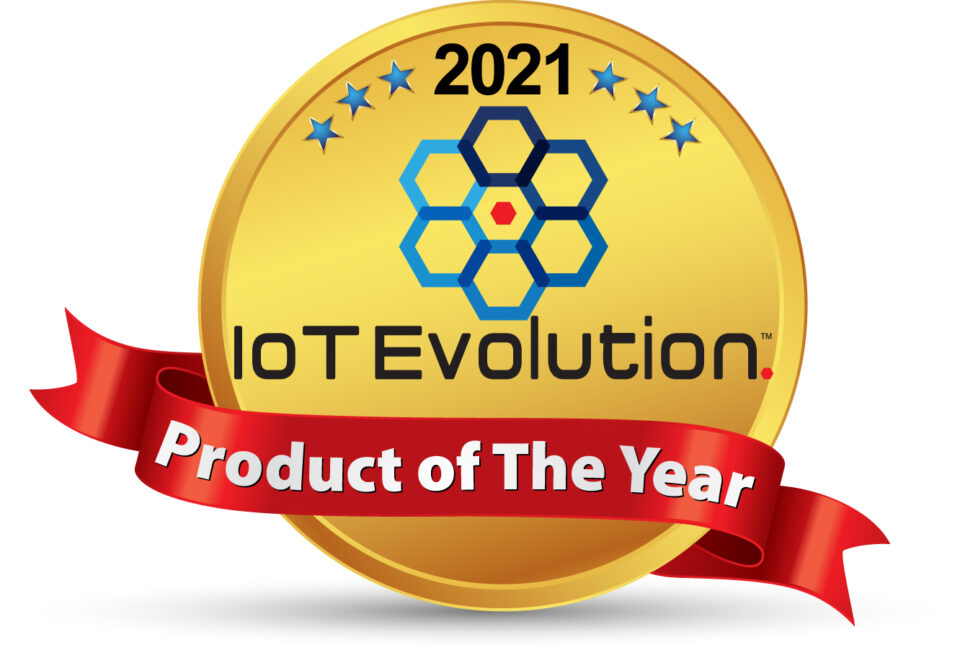
TMC Recognizes deviceWISE IoT Platform as the 2021 Product of the Year
Global media company TMC and its partner Crossfire Media named deviceWISE a winner of the 2021 IoT Evolution Product of the Year. This prestigious award recognizes the most innovative IoT products on the market.
ABI Research
ABI Research is another prestigious think tank that covers smart industrial platforms. They describe deviceWISE as follows:
“Compared to Kepware, deviceWISE has the advantage in lower latencies. Compared to FogHorn Systems, deviceWISE has more advanced IT/OT integration capabilities. Compared to homegrown data extraction and edge intelligence solutions provided by the industrial automation companies, deviceWISE has more flexibility and more advanced software.”
ABI Research, Smart Manufacturing Platform Ranking
See deviceWISE in Action
Honda and American Axle are two examples of companies that chose deviceWISE to address their top challenges and are reaping the rewards.
Honda Streamlines and Scales Operations
Honda, a leading automotive manufacturer, needed to improve its resource utilization and data quality. It wanted to streamline operations by increasing the commonality and compatibility across its tools and plants. The company was operating many major manufacturing applications on IBM mainframe and AIX platforms. These required custom code and middleware. The platforms were inflexible and performed poorly.
deviceWISE enabled Honda to integrate its applications seamlessly with the factory floor, including production PLCs from Omron, Mitsubishi, Siemens and Rockwell. The firm can take advantage of as-built quality data rather than requiring custom coding. After deploying deviceWISE, Honda was able to improve its efficiency and interoperability. It could scale its operations with ease to meet new market demands and ramp up new production facilities.
American Axle Improves Performance
American Axle, a global Tier 1 automotive supplier, has over 60 manufacturing facilities in 17 countries. The company has a strong focus on production build data and machine performance data collection. They sought to visualize and interpret this data to make more intelligent decisions.
American Axle initially relied on various ad hoc solutions. Their suppliers chose these off-the-shelf products to implement their systems. What they needed was a consistent data collection methodology. In 2001, American Axle co-developed and adopted a standard middleware layer and relied on OPC. Though they worked for some time, as their operations and data requirements grew, these systems became inadequate.
In the first quarter of 2015, American Axle turned to deviceWISE. They rapidly completed the first proof of concept in the second quarter and converted the first assembly line to deviceWISE by the third.
Among the many differences deviceWISE made for American Axle, the most crucial to them was performance. They switched from a single-threaded OPC application to a multi-threaded one, reducing response times from 893 to 126 milliseconds.
Bring Home the Big Win with deviceWISE
To survive in the competitive marketplace, manufacturers need to migrate to connected IoT manufacturing. We empower organizations to realize the potential of today’s technologies. We offer the world’s most comprehensive portfolio of high-performance IoT modules, connectivity services and software.
Long before IoT became fashionable, we were gaining extensive experience in connecting enterprise networks to machines. Our experts pioneered a successful end-to-end system approach. This approach assures each piece — device, connectivity and data management — operates seamlessly when connecting devices to apps. This experience is supported by a focus on removing barriers and risks to make onboarding IoT solutions simpler.
deviceWISE enables manufacturers to benefit from a manufacturing communications platform that is easy to integrate and change. It is accepted across an array of industries and used by a variety of OEMs. It empowers manufacturers to reap the advantages of a single, comprehensive solution.
deviceWISE operates on various computer platforms and in-rack systems, including:
- Microsoft Windows
- Linux
- IBM AIX
- Raspberry Pi
- Siemens
- Mitsubishi
- Rockwell
Designed for rapid deployment, deviceWISE decreases installation and maintenance costs. This platform eliminates intermediate PC technology, custom programming and homegrown solutions. With deviceWISE, manufacturers can reduce time to market by enabling connectivity that breaks through complicated data transfer layers.
Key Takeaways
- OPC is an aging standard that can’t keep up with the changing needs of today’s manufacturers.
- OPC is incompatible with many other technologies. Manufacturers seeking to integrate business and enterprise logic must purchase an OPC-compatible application or write custom code to create one.
- deviceWISE, powered by Telit Cinterion, is a comprehensive platform that far surpasses OPC. It offers hundreds of native drivers and a faster time to market. In addition, it offers out-of-the-box integration with your existing systems, so there’s no need to write custom code.