deviceWISE and AWS are used by one of the world’s largest tire manufacturers. With 19 manufacturing sites in 12 countries, the customer chose the deviceWISE and AWS combination to digitize its manufacturing plants.
The Challenge
In each of its multiple sites, the customer has various types of machines that speak different protocols and has more than one MES system. The customer’s objective was to digitize the manufacturing process and collect real-time machine data for factory performance visualization. The customer also wanted to add machine learning and data analytics to improve overall equipment effectiveness (OEE).
The Deployment
The customer selected deviceWISE to create standardization between the different machines and different IT systems. deviceWISE provides protocol translation so factories that run on Siemens, Rockwell or Mitsubishi controllers can be standardized with a unique protocol translation tool.
The customer also needed to collect data from external sensors, such as temperature sensors in the curing process. Telit deviceWISE has built-in interfaces for open protocols such as Modbus that make machine instrumentation an effortless process.
In addition to machine data and external instrumentation, the tire manufacturing process requires extensive quality control with full traceability. The full process data was collected and managed inside the deviceWISE platform by integrating deviceWISE with barcode readers. For the next step of the process, the customer added Telit deviceWISE VIEW dashboards for operators and managers. Since deviceWISE interconnected to the customer’s MES, they were able to create dashboards for quality control (e.g., comparing real process data to hypothetical optimum machine data) with drag-and-drop widgets.
AWS Connectivity
The customer’s extensive research showed that AWS would provide superior cloud functionalities, such as:
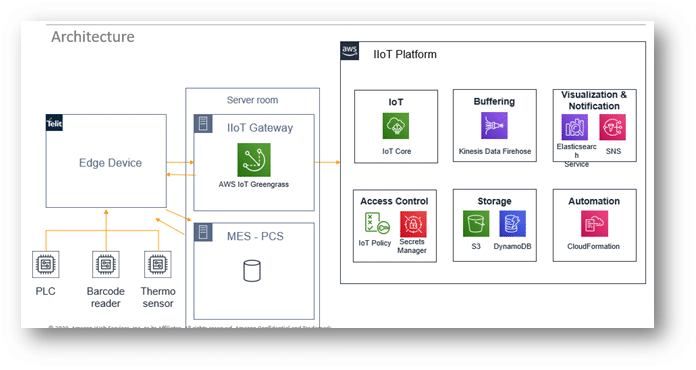
- Storage and data lake
- Data analytics
- Machine learning
The customer decided to standardize on AWS for cloud services and use Telit deviceWISE to provide an interface between machine data, MES and ERP.